MyFit TT
The 3D-printed socket for transtibial amputees from Ottobock, generated from a scan. Quick, clean and reproducible.
The 3D-printed socket for transtibial amputees from Ottobock, generated from a scan. Quick, clean and reproducible.
MyFit TT: 3D-printed socket
Orthotics and prosthetics professionals can now replace plaster with a 3D scanner and printer for the treatment of their users. This makes it possible to produce the first 3D-printed socket for transtibial amputees from Ottobock.
MyFit TT offers a complete digital solution: from scanning to software and 3D printing.
Inspired by the structure of human bones, the developers have created a socket that offers a high level of stability while using limited materials. This is made possible by a powder-based 3D printing process. Nylon powder gives the socket enough flexibility to put it on and take it off. It is also robust enough for daily use.
Future-proofing the industry through digitalisation
The new technology replaces manual production methods, particularly the processes of making a plaster cast of the residual limb, correcting the plaster model to make the socket mould or device, as well as actually producing the final socket. The socket is made in an additive manufacturing process and achieves the same quality as a conventionally produced socket. In the past, 3D-printed prosthetic parts often lacked the necessary stability. MyFit TT overcomes this challenge for a fully digitalised treatment process. The digital treatment process makes the patient experience in the medical supply company more pleasant while also reducing the level of work involved. This leaves more time for one-on-one conversations.
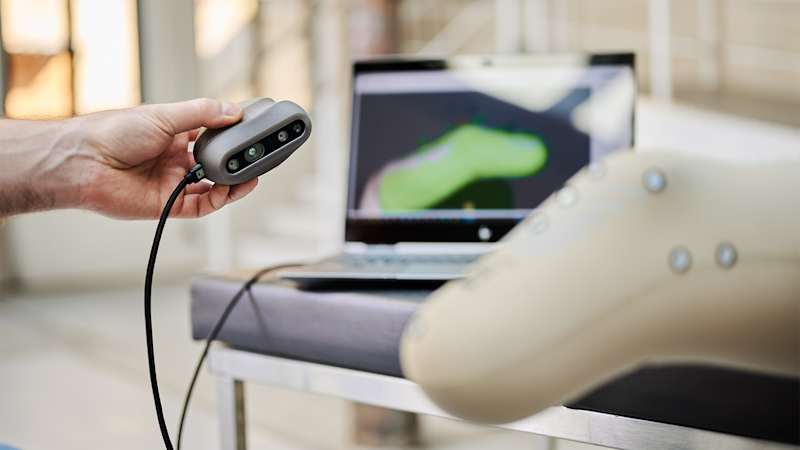
Advantages of additive manufacturing
Digital twin
Particular features of the residual limb, such as bony structures, can be marked, recorded with the scanner and shown in the modification software.
Reproducible
All of the processing steps are documented and can be reproduced. They can be adjusted and reversed at the touch of a button.
Protect resources
There is no need for a conventional plaster cast. The socket is printed without any model, ensuring less waste is generated.
Saves time
The technology replaces certain steps in the manual production process. This gives O&P professionals more time to work directly with the users.
Scan. Model. Print. Get the perfect fit in less time.
- 3D scan: A scanner is used to record images of the relevant body part from all sides (360°). This method is quicker and more comfortable than a plaster cast.
- Digital Modelling: By editing the scan in the software, the O&P professional creates the shape of the future socket.
- 3D-printing: The socket is produced in a 3D printer using a powder-based process.
- Fitting: The O&P professional checks the fit and the level of comfort.
How MyFit TT meets users’ needs
"The socket must fit well"
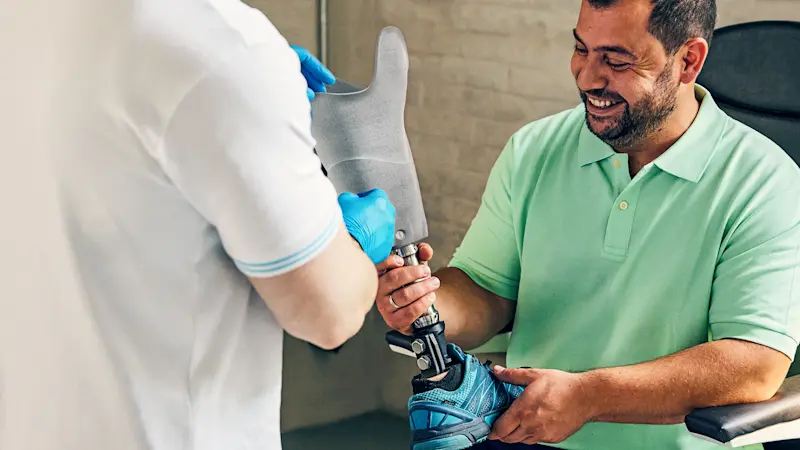
Beytullah Demir is one of the first people to wear the 3D-printed MyFit TT socket from Ottobock. He lost his lower leg in 2012 in a work accident. To ensure his prosthesis fits him well and does not cause pain at the residual limb, a perfectly customised socket is needed as the link between the person and the technology. This has to fit him like a glove. Today, Beytullah can go back to work, play football and train a team in his home town.
You love to be on the football pitch – while wearing your prosthesis. What does that mean for you after your amputation?
I have played football ever since I was little. I am now a coach and player at the same club. For me to achieve that following my amputation is a miracle.
What makes you feel proud?
My accident brought the important things in life to the fore for me. It woke me up, because you understand that your life could end overnight. I bought a house, married my girlfriend and had children. She wanted to do it – at the time, we had been together for nine years and I had always thought it was too soon. All we argue about now are the little things. I’m just very happy in my life.
How did you find out that your lower leg needed to be amputated?
I woke up in the hospital and, to be honest, I can remember very little of the first few days in intensive care. I thought I was in hospital near Höxter but the nurse told me I was at the university hospital in Göttingen. I knew that you only go to Göttingen if you have something serious. The chief physician told me I had lost the blood supply to my foot and he recommended an amputation. He did not think my foot would recover.
How did you react?
First, I wanted to find a clinic that would save my foot. But the risk of sepsis was much higher. After an odyssey through various hospitals, I had to make a decision. I was tearing my hair out, I was so distraught. Fortunately, the windows at the hospital in Göttingen are closed because I considered jumping out. Then I decided to have my lower leg amputated. They moved me to the operating theatre and I started to cry. I knew that when I came out, I would be coming out without a leg. Then I said goodbye to my leg.
What was it like in the period after your amputation?
I lifted up the blanket and that was when I started going through a difficult phase mentally. But my doctor was there for me day and night. He told me: “You have two options: either you get up and fight for your life or tomorrow morning you come to the psychiatric ward next door.”
What did that do to you?
After that conversation, I thought: come on, get up! You can jump out of the window any time. I let people back into my life. My room looked like a flower shop. There were lots of people there who I never expected to see. In the end, I needed every one of them. That gave me strength; I started to participate in life again.
What was your initial period with a prosthesis like?
Ottobock came to my home and I was given initial treatment. I then spent six weeks as an inpatient in rehabilitation. I heard stories there that were more tragic than my own, and I realised that I wanted to be able to do everything as I could before. After three weeks, I stopped using crutches. Then, in September 2013, I started working in my old job again.
You were fitted with a 3D-printed socket. How does it differ from a conventional plaster cast and socket?
I was the first user to be scanned in Duderstadt. I think 3D printing is brilliant because it’s more pleasant and doesn’t involve all of that plaster – so it’s better for the environment too. My professional scans me and brings me the socket a few days later. I put it on and it fits. I would have no problem if all of my prostheses were 3D-printed. It’s ready sooner, and it’s cleaner and more comfortable.
How would you describe that? How much faster is 3D printing?
With a plaster cast, the professional is done in half an hour. With 3D scanning, it takes ten minutes, if that – you just go round once.
Does a socket from a 3D printer feel different?
I can bend more easily with my socket. It’s important to me that the socket is a good fit. Otherwise, even the best prosthesis will be useless. All of the sockets made through 3D printing have had a really good and secure fit. As if they are part of me. I’m very happy and that’s a great feeling.
Contact person
Additional topics
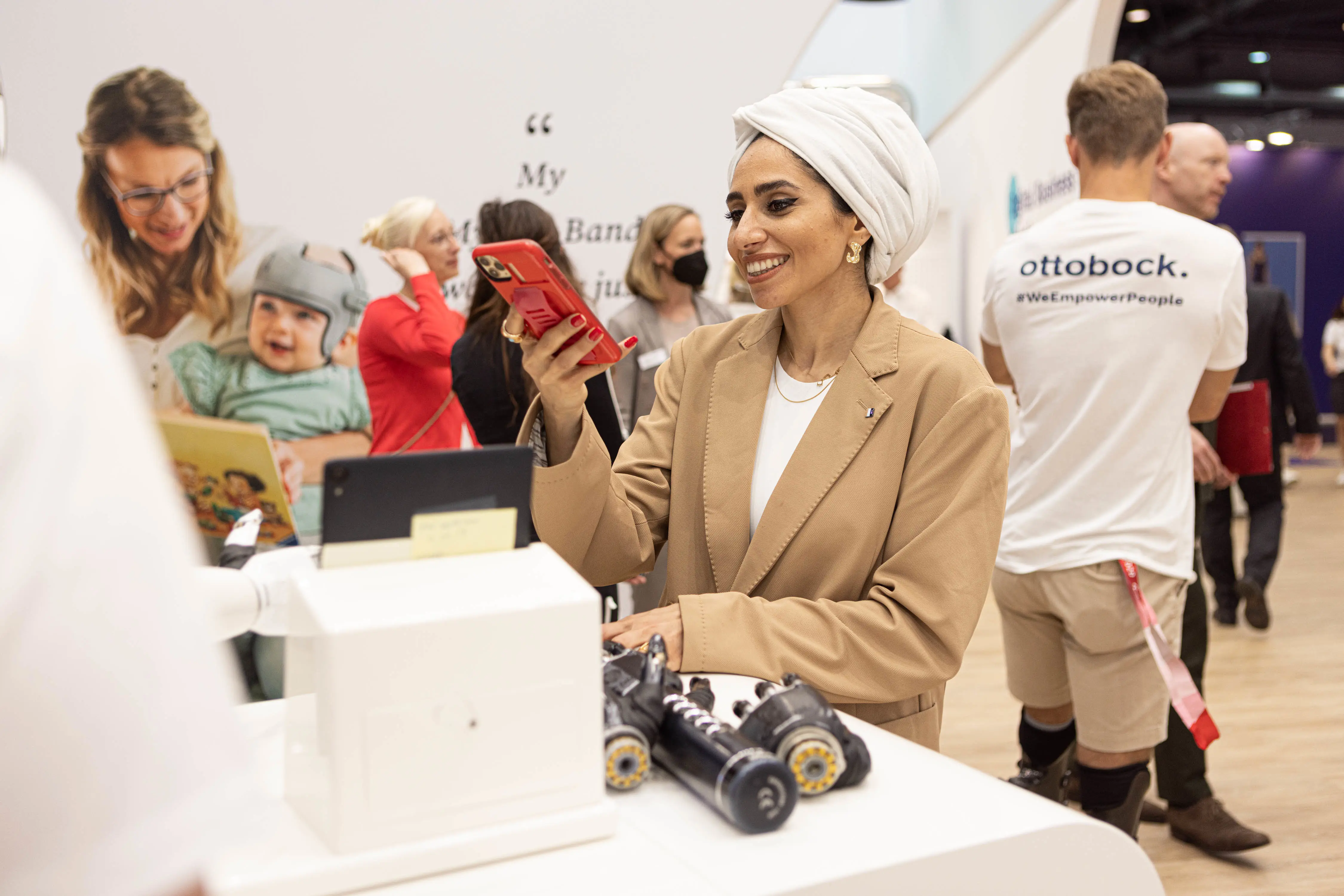
Media information
Would you like to know more about our product highlights? Do you need high-resolution images for your publication? We have compiled product information and images for journalists here.
Would you like to know more about our product highlights? Do you need high-resolution images for your publication? We have compiled product information and images for journalists here.
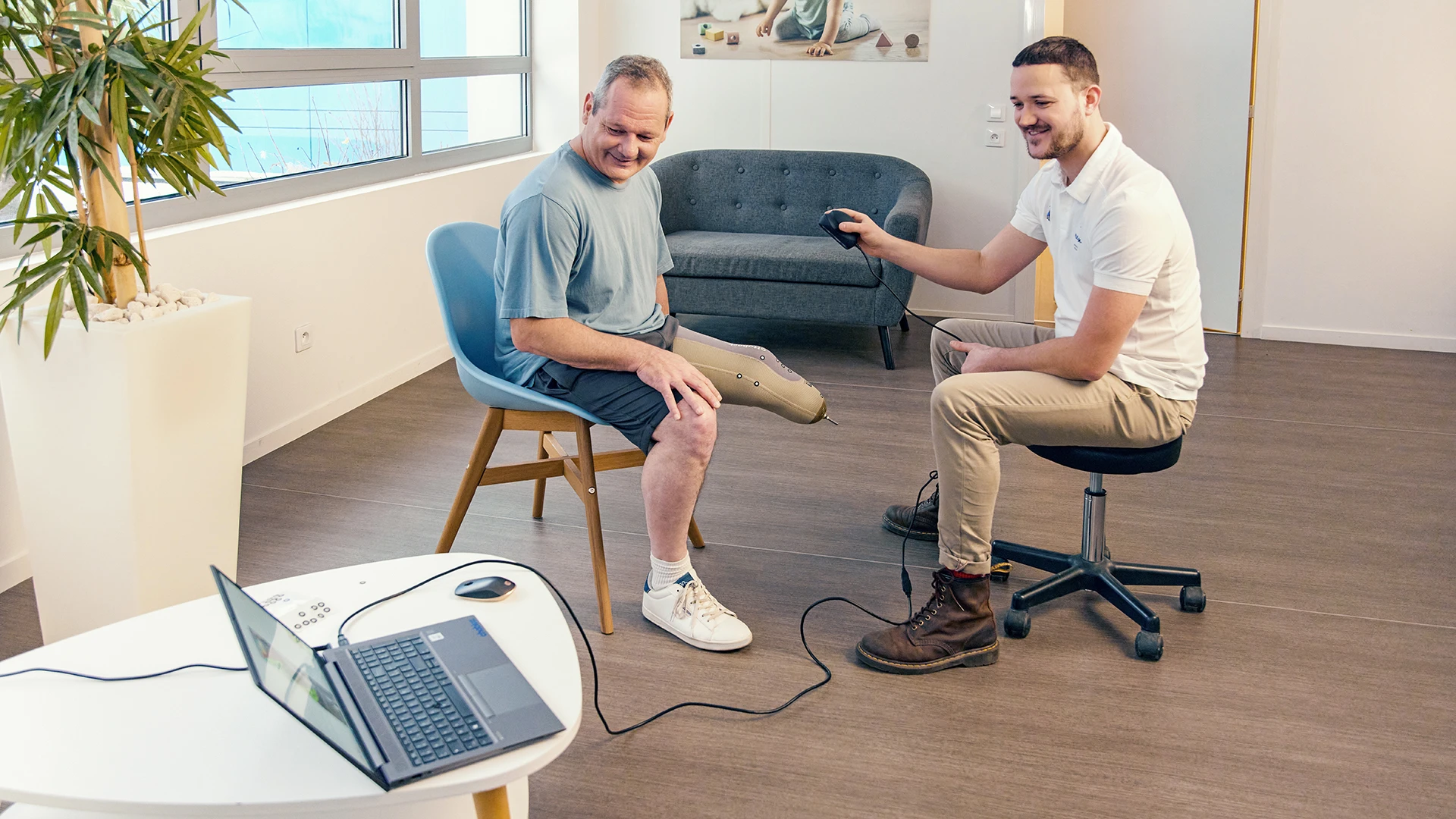
How 3D scanners and printers are revolutionising fitting for patients
Fast and customized production is the future of orthopedic technology. The iFab has digitized the complete fitting and production process.
Fast and customized production is the future of orthopedic technology. The iFab has digitized the complete fitting and production process.
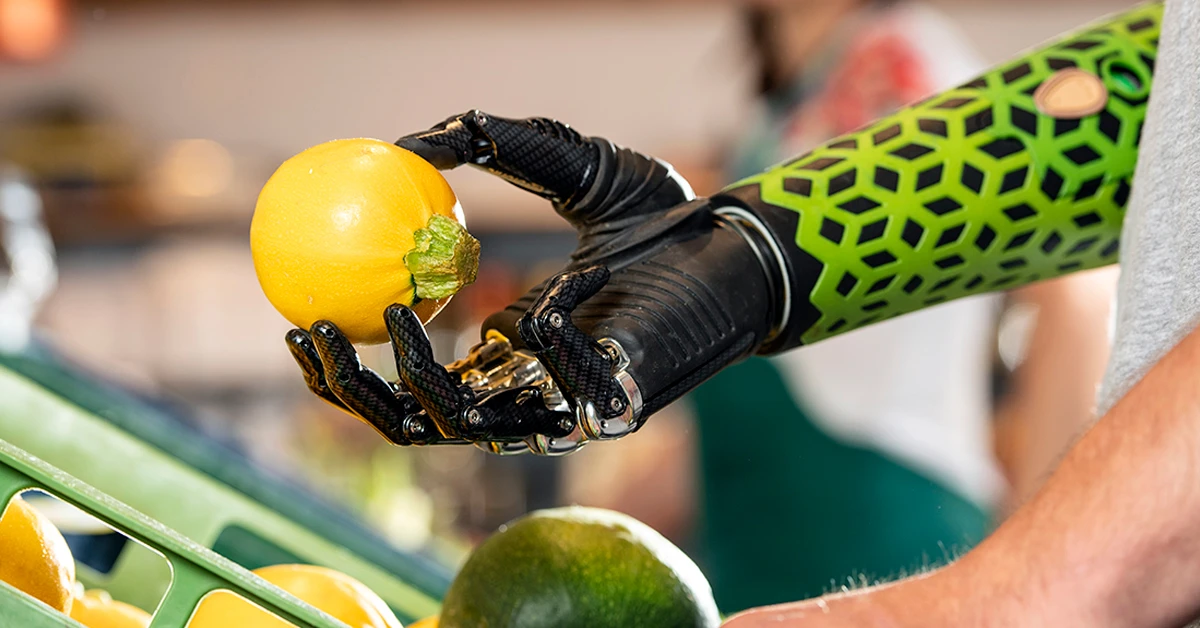
Myo Plus pattern recognition
3 results out of 3